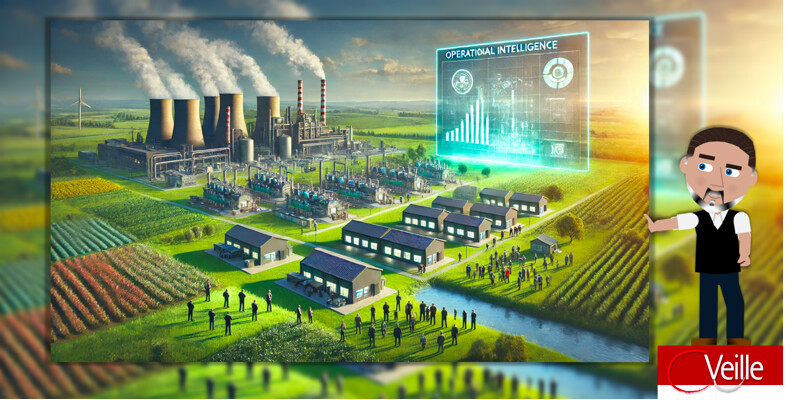
France is experiencing a period of deindustrialization marked by factory closures affecting entire sectors. In November 2024, Michelin announced the closure of its Cholet and Vannes sites, leaving 1,250 employees facing a grim reality. In Brussels, the Audi factory is also under threat, prompting unions to propose a social plan to save jobs. These closures are turning once-thriving production sites into industrial wastelands and plunging entire regions into an economic and social impasse. Faced with this crisis, local elected officials and economic stakeholders need to rethink the ecosystem to prevent economic desertification. The needs are urgent, requiring rapid and effective solutions. This is where the concept of decentralized mini-factories, supported by Operational Competitive Intelligence (IC Ops), emerges as a realistic solution.
Small, autonomous, and flexible industrial structures, mini-factories have the potential to revive local production. By incorporating economic intelligence with a highly operational approach, they maximize local resources, both human and material, in a frugal and efficient way. Rather than relying on large, costly installations, they prioritize agility and efficiency, optimizing every function to maximize impact while minimizing investment. The concept of mini-factories thus positions itself as an alternative to globalized supply chains. They produce closer to demand, reduce logistical costs, and adapt production in real-time. For regions, they represent a chance to regain industrial autonomy, diversify activities, and create sustainable jobs, responding directly to the challenges posed by factory closures. However, an “entrepreneurial/innovative” mindset is essential to identify actionable steps for deploying such solutions while limiting delays and heavy investments.
Small, autonomous, and flexible industrial structures, mini-factories have the potential to revive local production. By incorporating economic intelligence with a highly operational approach, they maximize local resources, both human and material, in a frugal and efficient way. Rather than relying on large, costly installations, they prioritize agility and efficiency, optimizing every function to maximize impact while minimizing investment. The concept of mini-factories thus positions itself as an alternative to globalized supply chains. They produce closer to demand, reduce logistical costs, and adapt production in real-time. For regions, they represent a chance to regain industrial autonomy, diversify activities, and create sustainable jobs, responding directly to the challenges posed by factory closures. However, an “entrepreneurial/innovative” mindset is essential to identify actionable steps for deploying such solutions while limiting delays and heavy investments.
Competitive Intelligence Operation : agility and efficiency for mini-factories
For mini-factories to function effectively, they require an agile and efficient strategy. This is where Operational Competitive Intelligence (IC Ops) comes in. This new concept integrates the application of competitive intelligence at every stage of production and throughout the supply chain, enabling optimal management of resources and costs. It is based on a simple vision: using data, strategic information, and stakeholder networks to adjust operations in real-time, maximizing responsiveness and minimizing expenditure.
IC Ops begins with targeted monitoring that is closely aligned with the operational needs of the business. This monitoring process tracks trends and the specific needs of each territory, thus avoiding unnecessary investments. It identifies weak signals in local demand, regulatory changes, and market opportunities, enabling mini-factories to adapt without wasting resources. This anticipation allows factories to adjust production to the precise needs of local clients, limiting stockpiles and maximizing efficiency.
IC Ops begins with targeted monitoring that is closely aligned with the operational needs of the business. This monitoring process tracks trends and the specific needs of each territory, thus avoiding unnecessary investments. It identifies weak signals in local demand, regulatory changes, and market opportunities, enabling mini-factories to adapt without wasting resources. This anticipation allows factories to adjust production to the precise needs of local clients, limiting stockpiles and maximizing efficiency.
Next, IC Ops emphasizes the optimization of local resources. Rather than relying on distant suppliers or costly materials, mini-factories utilize skills and materials available locally. By collaborating with local partners, they reduce transportation costs and minimize the risk of supply chain disruptions. This short-circuit production not only lowers expenses but also benefits the local economy. If immediate access to resources is not possible nearby, an alternative approach is systematically considered.
Finally, IC Ops offers unprecedented operational flexibility. By incorporating competitive intelligence into production and logistics processes, mini-factories can adjust their functions based on the evolving needs of their territory. If demand changes, they adapt. If a new need arises, they can address it swiftly, demonstrating agility. This responsiveness is a crucial asset in an unstable economic environment. This approach maximizes impact while controlling costs, addressing real-world conditions without unnecessary complexity.
Finally, IC Ops offers unprecedented operational flexibility. By incorporating competitive intelligence into production and logistics processes, mini-factories can adjust their functions based on the evolving needs of their territory. If demand changes, they adapt. If a new need arises, they can address it swiftly, demonstrating agility. This responsiveness is a crucial asset in an unstable economic environment. This approach maximizes impact while controlling costs, addressing real-world conditions without unnecessary complexity.
Enhancing Skills: a transfer to new sectors
One of the major challenges of factory closures is the loss of specialized skills. Hundreds of workers trained in automotive, metallurgy, or agri-food trades suddenly find themselves unemployed. Yet their skills have value and can be redirected. Decentralized mini-factories, supported by IC Ops, offer a solution not only to preserve but also to transform these skills into new opportunities.
These mini-factories allow for a transfer of skills to growing sectors. These skills can be adapted to expanding fields such as additive manufacturing, the circular economy, or renewable energy. Instead of letting these skills go to waste, mini-factories harness them in future-oriented industries. This model also relies on the rapid and targeted retraining of employees.
With support from local training centers, mini-factories could implement customized training programs directly aligned with their production needs. Employees thus benefit from rapid skills development, allowing them to apply their expertise in modernized environments, such as 3D printing or electronic component assembly.
Lastly, mini-factories create cross-sector synergies. By bringing together skills from various fields, they foster local innovation. A former automotive technician can work alongside a sustainable materials expert to develop new products or more environmentally-friendly production methods. This diversity of skills, concentrated within a single space, stimulates creativity and boosts the competitiveness of territories.
This skill transfer is a realistic response to the challenges of deindustrialization. By enabling workers to reinvent themselves without abandoning their expertise, mini-factories contribute to creating a more resilient, innovative local economy that is better suited to current challenges
These mini-factories allow for a transfer of skills to growing sectors. These skills can be adapted to expanding fields such as additive manufacturing, the circular economy, or renewable energy. Instead of letting these skills go to waste, mini-factories harness them in future-oriented industries. This model also relies on the rapid and targeted retraining of employees.
With support from local training centers, mini-factories could implement customized training programs directly aligned with their production needs. Employees thus benefit from rapid skills development, allowing them to apply their expertise in modernized environments, such as 3D printing or electronic component assembly.
Lastly, mini-factories create cross-sector synergies. By bringing together skills from various fields, they foster local innovation. A former automotive technician can work alongside a sustainable materials expert to develop new products or more environmentally-friendly production methods. This diversity of skills, concentrated within a single space, stimulates creativity and boosts the competitiveness of territories.
This skill transfer is a realistic response to the challenges of deindustrialization. By enabling workers to reinvent themselves without abandoning their expertise, mini-factories contribute to creating a more resilient, innovative local economy that is better suited to current challenges
Responding to the realities of a globalized market: adaptation and entrepreneurial support
For mini-factories to succeed, they must adapt to the realities of an increasingly globalized market. Local production is a solution, but it is not enough. These lightweight and flexible structures must also be competitive beyond their territory and meet high-quality standards.
To achieve this, they need targeted entrepreneurial support and a strategy aligned with global requirements while remaining rooted in local specifics. Entrepreneurial support is essential. Mini-factory creators must be backed by stakeholders such as chambers of commerce, regional incubators, and economic development agencies.
This support aims to structure their business model, identify profitable market segments, and adjust operations to meet the expectations of both local and international clients. This includes managing costs, enhancing quality, and targeting specific niches with growth potential. Action and cooperation within territorial actor networks are necessities.
To achieve this, they need targeted entrepreneurial support and a strategy aligned with global requirements while remaining rooted in local specifics. Entrepreneurial support is essential. Mini-factory creators must be backed by stakeholders such as chambers of commerce, regional incubators, and economic development agencies.
This support aims to structure their business model, identify profitable market segments, and adjust operations to meet the expectations of both local and international clients. This includes managing costs, enhancing quality, and targeting specific niches with growth potential. Action and cooperation within territorial actor networks are necessities.
Mini-factories must also develop niche strategies to stand out in the global market. Through IC Ops, they can identify high-value niches where they can offer unique products tailored to specific demands. For example, a mini-factory specializing in additive manufacturing might target cutting-edge industries like medical or aerospace, which require technically complex and customized production that is difficult to achieve on a large scale.
Finally, compliance with global standards is a decisive asset. IC Ops enables monitoring and anticipating changes in quality standards, certifications, and international regulatory requirements. Mini-factories can thus adjust their processes and ensure their products meet global standards. This adaptability is crucial for integration into international value chains, even while remaining a local structure. For territories, this translates to new economic opportunities, export potential, and sustainable value creation, drawing on local resources and skills.
Conclusion: toward a new Industry for Territories, supported by adapted financing
Supported by Operational Competitive Intelligence (IC Ops), mini-factories offer a realistic path to revitalize local industry and address current economic challenges. Concrete examples from France, Scandinavia, and Germany, where short-circuit production structures and specialized factories have been successfully implemented, demonstrate that it is possible to combine innovation and flexibility to create jobs and strengthen the local economy.
However, for this mini-factory model to be scaled up, adapted financing is essential. Rather than requiring massive investments, these lightweight structures benefit from diverse, accessible financial solutions such as microcredits, crowdfunding, cooperative partnerships, and public-private collaborations. By incorporating these flexible funding sources, territories can minimize risks and quickly mobilize local resources, ensuring that every invested dollar generates a direct impact.
The option to start with small-scale pilot projects offers regions a realistic roadmap to test, adjust, and strengthen their industrial initiatives. With precise success indicators—jobs created, local investments, market access—decision-makers can monitor the model’s effectiveness and optimize it. This agile, localized financing approach enables mini-factories to be durably rooted in territories, making them competitive and integrated into international value chains.
This hybrid model, combining lean financing and flexible production, represents a unique opportunity to create a resilient and sustainable local industry. As pillars of economic recovery, these mini-factories could transform territories currently in crisis into engines of innovation and development, with measurable impacts on employment, the economy, and competitiveness.
However, for this mini-factory model to be scaled up, adapted financing is essential. Rather than requiring massive investments, these lightweight structures benefit from diverse, accessible financial solutions such as microcredits, crowdfunding, cooperative partnerships, and public-private collaborations. By incorporating these flexible funding sources, territories can minimize risks and quickly mobilize local resources, ensuring that every invested dollar generates a direct impact.
The option to start with small-scale pilot projects offers regions a realistic roadmap to test, adjust, and strengthen their industrial initiatives. With precise success indicators—jobs created, local investments, market access—decision-makers can monitor the model’s effectiveness and optimize it. This agile, localized financing approach enables mini-factories to be durably rooted in territories, making them competitive and integrated into international value chains.
This hybrid model, combining lean financing and flexible production, represents a unique opportunity to create a resilient and sustainable local industry. As pillars of economic recovery, these mini-factories could transform territories currently in crisis into engines of innovation and development, with measurable impacts on employment, the economy, and competitiveness.
If this topic interests you and you would like more details, please feel free to contact Veille Mag - jsala@veillemag.com
- so that we can provide more in-depth articles on specific points discussed here.